The Basic Principles Of Alcast Company
The Basic Principles Of Alcast Company
Blog Article
All About Alcast Company
Table of ContentsFascination About Alcast CompanyAll about Alcast Company6 Simple Techniques For Alcast CompanyThe 45-Second Trick For Alcast CompanyFascination About Alcast CompanyAlcast Company Can Be Fun For Everyone
Chemical Comparison of Cast Light weight aluminum Alloys Silicon advertises castability by decreasing the alloy's melting temperature and boosting fluidness throughout casting. Furthermore, silicon adds to the alloy's toughness and wear resistance, making it important in applications where durability is essential, such as automotive components and engine parts.It also boosts the machinability of the alloy, making it less complicated to refine right into completed items. This way, iron contributes to the general workability of aluminum alloys. Copper boosts electric conductivity, making it useful in electric applications. It also boosts corrosion resistance and includes in the alloy's overall toughness.
Manganese adds to the strength of aluminum alloys and boosts workability (aluminum foundry). It is commonly utilized in functioned aluminum items like sheets, extrusions, and profiles. The existence of manganese aids in the alloy's formability and resistance to breaking during fabrication procedures. Magnesium is a lightweight aspect that supplies toughness and effect resistance to aluminum alloys.
Alcast Company for Dummies
It enables the manufacturing of light-weight components with outstanding mechanical residential properties. Zinc boosts the castability of aluminum alloys and aids control the solidification procedure during spreading. It boosts the alloy's toughness and firmness. It is frequently found in applications where elaborate shapes and great details are essential, such as decorative castings and specific automobile components.

The main thermal conductivity, tensile toughness, return toughness, and prolongation differ. Select ideal basic materials according to the performance of the target item created. Amongst the above alloys, A356 has the highest possible thermal conductivity, and A380 and ADC12 have the cheapest. The tensile limit is the contrary. A360 has the most effective yield strength and the greatest prolongation rate.
The Of Alcast Company
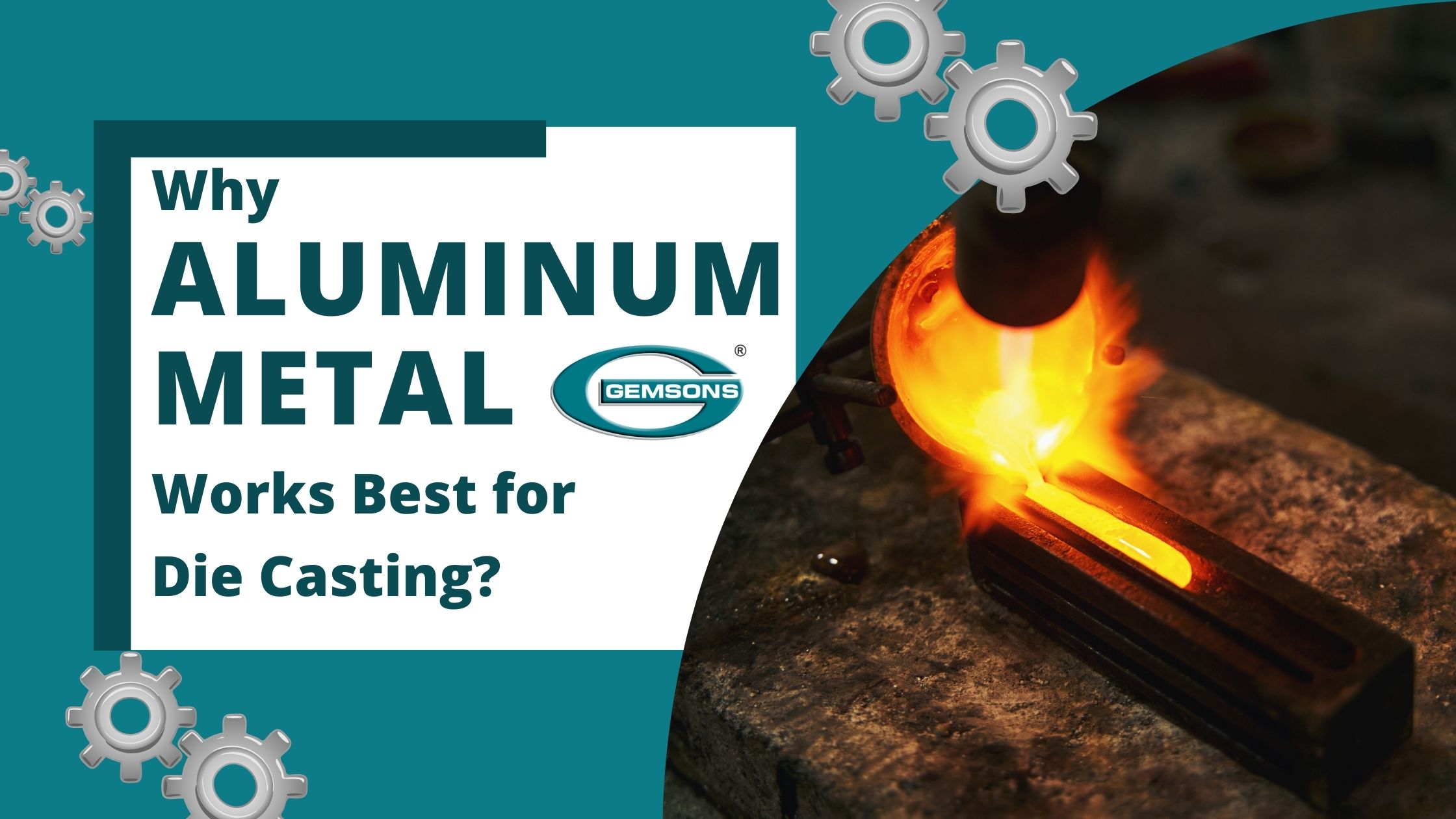
In accuracy casting, 6063 is well-suited for applications where detailed geometries and top notch surface coatings are paramount. Instances include telecommunication units, where the alloy's superior formability permits smooth and cosmetically pleasing designs while maintaining architectural stability. In the Lights Solutions market, precision-cast 6063 parts produce classy and effective illumination components that call for elaborate forms and excellent thermal efficiency.
It causes a better surface coating and much better rust resistance in A360. The A360 exhibits exceptional elongation, making it optimal for complicated and thin-walled components. In precision casting applications, A360 is fit for markets such as Consumer Electronics, Telecommunication, and Power Devices. Its boosted fluidity allows for complex, high-precision elements like smartphone housings and interaction device real estates.
Top Guidelines Of Alcast Company
Its distinct homes make A360 an important choice for precision casting in these industries, enhancing product sturdiness and top quality. Foundry. Light weight aluminum alloy 380, or A380, is a commonly made use of casting alloy with several distinct attributes.
In accuracy spreading, aluminum 413 shines in the Consumer Electronics and Power Devices industries. It's typically made use of to craft intricate components like mobile phone housings, cam bodies, and power tool casings. Its accuracy is impressive, with limited tolerances as much as 0.01 mm, guaranteeing perfect item assembly. This alloy's remarkable deterioration resistance makes it an outstanding option for outside applications, guaranteeing lasting, resilient products in the mentioned industries.
The 7-Second Trick For Alcast Company
The light weight aluminum alloy you select will substantially impact both the casting procedure and the buildings of the final product. Since of this, you need to make your decision thoroughly and take an educated technique.
Determining the most suitable aluminum alloy for your application will certainly imply evaluating a broad selection of characteristics. The first group addresses alloy features that influence the manufacturing process.
Not known Facts About Alcast Company
The alloy you choose for die casting directly affects several aspects of the spreading process, like just how easy the alloy is to deal with and if it is prone to casting flaws. Warm splitting, also understood as solidification fracturing, his comment is here is a normal die casting defect for light weight aluminum alloys that can cause inner or surface-level rips or splits.
Particular light weight aluminum alloys are a lot more susceptible to hot breaking than others, and your option must consider this. It can damage both the actors and the die, so you must look for alloys with high anti-soldering residential properties.
Rust resistance, which is currently a remarkable feature of aluminum, can differ substantially from alloy to alloy and is an important characteristic to consider depending upon the ecological problems your item will be revealed to (aluminum foundry). Use resistance is one more building frequently looked for in aluminum items and can differentiate some alloys
Report this page